Source: NASA.
If you're following 3D Systems (DDD 3.33%), Stratasys (SSYS 0.52%), or the 3D printing space in general, you're likely aware of the main hurdles that are holding back 3D printing from making faster inroads into the manufacturing environment. These include speed, materials capabilities, and built-in quality assurance measures. NASA just overcame one huge part of the "materials capabilities" challenge by 3D printing the first real-life composite part -- a mirror mount made of several different alloys.
Let's look at NASA's accomplishment and its potential implications.
3D printing mission accomplished
Researchers from NASA's Jet Propulsion Laboratory, Caltech, and Penn State have developed a 3D printing process that transitions from one metal or alloy to another as a single object is being printed. This enabled them to 3D print a spacecraft mirror mount that is composed of several different alloys.
NASA's accomplishment marks the first time 3D printing has been used to produce a single object made of different metals or alloys, according to John Paul Borgonia, a JPL mechanical engineer. Gradient alloys have been created in the past, though they've been limited to research and development settings.
Why would NASA (or others, for that matter) need to make such a machine part in this manner? Its press release says it well:
Say you want a metal object where you would like the ends to have different properties. One side could have a high melting temperature and the other a low density, or one side could be magnetic and the other not. Of course, you could separately make both halves of the object from their respective metals and then weld them together. But the weld itself may be brittle, so that your new object might fall apart under stress. That's not a good idea if you are constructing an interplanetary spacecraft, for example, which cannot be fixed once it is deployed.
This new technique involves depositing layers of metal on a rotating rod, which allows for transitioning the metals from the inside out. The traditional 3D printing technique involves adding layers from bottom to top to create an object. A laser -- or sometimes an electric beam -- melts the metal powder to create the layers.
"We're taking a standard 3D printing process and combining the ability to change the metal powder that the part is being built with on the fly," Douglas Hofmann, a JPL researcher and visiting associate at Caltech, said in the press release. "You can constantly be changing the composition of the material."
One huge leap for 3D printing technology
NASA's accomplishment removes one huge hurdle that has been holding back metal 3D printing from increased use in production applications, as many components are composed of more than one metal or alloy. When we narrow this down to low-run specialty production applications, the obstacle removed is even bigger. That's because production speed -- another major complication -- doesn't matter much when making just one or a few very high-end specialty components, such as NASA might produce for a spacecraft.
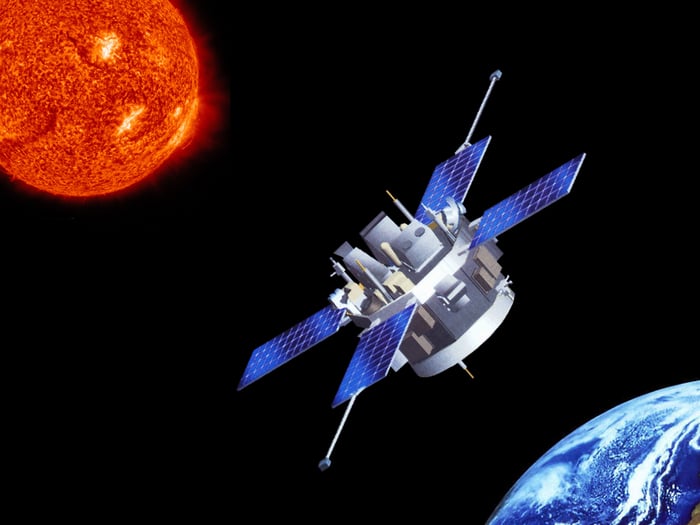
Source: NASA.
According to NASA, future space missions might incorporate parts made using this new technique. The auto and commercial aerospace industries might also find it useful, noted Hofmann. So it seems likely that this new 3D printing technology could increase the already out of this world growth projections for the 3D printing industry. According to the 2014 Wohlers Report -- widely considered the gold standard on the industry -- revenue for the market grew by 35% year over year to approximately $3 billion in 2013. Wohlers projects that the market will explode to $10.8 billion in 2021. Morgan Stanley is even more optimistic, as its bull scenario predicts the 3D printing industry to be worth $21 billion by 2020.
The press release included no information regarding the specific 3D printer used to produce the multialloy component. I'd assume that NASA started with a standard model and modified it. The release did mention "lasers," so it seems a printer based on selective laser sintering was used, rather than one using electron beam melting technology. 3D Systems is the only publicly traded company that makes metal printers that use laser sintering technology. However, some well-regarded private companies also make these types of metal printers. Germany-based EOS is frequently cited as a very high-quality player in this space. Arcam (NASDAQOTH: AMAVF) is the only company that makes metal printers that use EBM tech, which is a patent-protected proprietary technology.
The threat NASA's new technology presents to 3D Systems, Strayasys, and the other 3D printing companies is unknown at this point. I'll be following this story to see if we can learn what model printer was used, what's the patent situation, and if NASA has been partnering or plans to partner with any 3D printing companies on this technology. Based on the limited information available, my initial take is that the method NASA used sounds general enough that other 3D printing companies will be able to use a similar method to produce systems that are also capable of printing in multialloys.
Bringing it all home... or back to Earth
Demand for 3D printers that can print in metals is in the relatively early stages, and we're on the cusp of an incredible growth trajectory. While it's too soon to say how NASA's new development might alter the 3D printing competitive landscape, it seems highly likely that it will help turbocharge the technology's disruption of traditional manufacturing.