When it comes to business, efficiency is valuable. But being efficient and doing it in a way that also keeps an eye on your customer is a whole different challenge. Enter Six Sigma, a process designed to help you do just this.
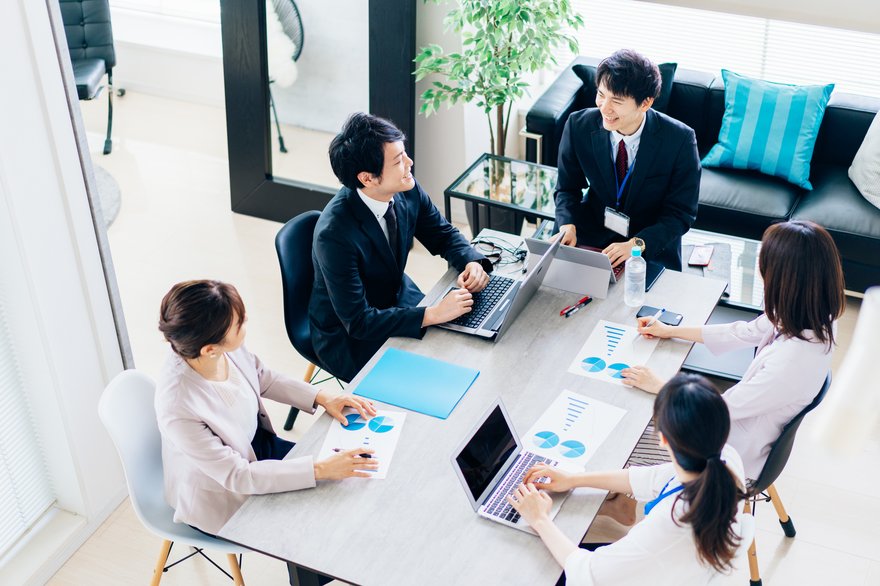
Definition
What is Six Sigma?
Six Sigma is a system of techniques and tools that can help business logistics run more efficiently and effectively. Through the use of statistics, defects can be identified, their causes detected and worked on, and the potential for a new occurrence of the same or similar problem reduced dramatically.
Bill Smith initially developed Six Sigma in 1986 at Motorola (MSI -0.73%) as a way of increasing business performance in a tough economic environment, and it ended up being a big hit among company leaders across the globe. Leaders like Jack Welch, chairman of General Electric (GE 0.68%) in the 1990s, realized a significant return on investment from Six Sigma, and it became a standard for many industries.
Principles
The principles of Six Sigma
Six Sigma is a set of processes, united by five main principles that help a user navigate their way through problem-solving. These principles are:
- Focus on the customer. Six Sigma is about maximizing the benefits and appeal for customers. If the business can't understand their customers -- and how and why they use a product or service -- they can't understand how to fix the issues at hand.
- Locate the problem. Defining goals for data collection, data gathering, and anticipated insights helps to expedite the necessary deep dive into the processes involved, as well as the supply chains that feed them.
- Eliminate defects. Using gathered data is the best way to find problems that can then be solved. Action plans can be built from the data to eliminate defects and outliers to improve processes overall.
- Involve stakeholders. If everyone who has a stake in the process has a hand in solving the problem, it's far more likely to succeed. Stakeholders that include suppliers and employees must be equal partners in fixing issues, or they won't stay fixed for long.
- Encourage a flexible environment. Change happens constantly when using a Six Sigma approach. A flexible environment is needed. Departments, employees, and environments have to be responsive to use Six Sigma effectively.
Steps
What are the steps in Six Sigma?
Once the principles of Six Sigma are established, you can focus on the actual process. There are two different ways to approach Six Sigma: DMAIC and DMADV. Here are their steps.
DMAIC
DMAIC is about improving business processes and management. It's an acronym for the steps involved, which are:
- Define the problem and your goals.
- Measure the existing parameters of the current problem.
- Analyze the data to find the flaws in the process.
- Improve the process using that data.
- Control the way the process is implemented to eliminate or reduce the problem.
DMADV
DMADV is similar to DMAIC, but instead of focusing on fixing existing business processes, it is about developing new business processes, products, or services to solve problems. Often, DMADV comes in when DMAIC has failed, and a process must be designed from scratch rather than retooled to work better.
The first three steps are basically the same as DMAIC, but the last two are very different:
- Define the problem and your goals.
- Measure the parameters of the current problem.
- Analyze the data to find the flaws in the process and develop alternatives.
- Design the best alternative and test the prototype.
- Verify the design's effectiveness (using simulations and pilot programs).
Related investing topics
Why use it?
Why use Six Sigma?
Six Sigma sounds rigorous and may be enough to put some people off, but it actually helps both employees and employers in many ways. By reducing waste and increasing efficiency, the company can increase revenue for itself and its shareholders, as well as improve customer satisfaction.
For employees, Six Sigma training can lead to better opportunities, more pay, improved job security, and more job opportunities elsewhere if they choose to leave a company where they've been Six Sigma certified. Because it's such a widespread standard, Six Sigma-trained workers are really in demand.