About a year and a half ago, Colorado resident and inventor David Hartkop unveiled the Mini Metal Maker, the world's first desktop 3D printer for metal. Not only did the prototype appear to have potential, but Hartkop also gave the world a first-hand glimpse at the fast-growing maker culture, or do-it-yourself 3D printing aficionados -- an eye-opener for those who have never touched a 3D printer. Since then, this interesting contraption has gone from prototype to production version, and Hartkop is now looking to bring the printer to market.
Mini Metal Maker. Source: David Hartkop.
In another exclusive interview with Hartkop, The Motley Fool again gets the first close look at this interesting desktop printer.
What is the Mini Metal Maker?
Built out of steel and aluminum, and featuring unique 1-pending technologies, Hartkop describes the Mini Metal Maker as bringing together the worlds of 3D printing and metal clay.

Bronze gears printed from open source files for REPRAP Wade extruder using Mini Metal Maker. Source: David Hartkop.
"The Mini Metal Maker prints 3D objects from digital files directly in metal clay, rather than in plastic. Once these clay objects air-dry, they are fired in a kiln to produce beautiful solid metal objects of high purity and precision," Hartkop said.
Key to the Mini Metal Maker's value proposition to craft makers, Hartkop emphasizes that the Mini Metal Maker's use of metal clay replaces the lost-wax process ordinarily needed to produce metal objects.
The printing space is small, but precise. The print bed currently allows for prints up to a 3.15-inch cube, or 8 x 8 x 8 cm. The positioning precision is 10 microns, virtually identical to Stratasys' (SSYS 5.47%) MakerBot. Layer resolution is 150 microns -- precise enough for intricate metal items like small bezel settings or jewelry details.
Hartkop envisions a range of uses for the Mini Metal Maker:
The Mini Metal Maker is the perfect tool for the artisan, artist or DIY maker. 3D printing with metal clay makes fabrication in metal easy and direct. It will be a boon for anyone interested in creating custom printing jewelry and metal ornaments. It can also be used to produce small metal parts such as gears, clips, and bushings.
What's new?
From a stronger extruder section to auto leveling, there are a number of key improvements in the production version of the Mini Metal Maker. In the video below, Hartkop explains all of the improvements in the newest version.
Further, with the Mini Metal Maker ready to be manufactured, Hartkop has also narrowed down the software that will be used. Users can run all of Mini Metal Maker's features with open-source software, Hartkop said.
For instance, we've been using Slic3r to bring in .stl files and slice them and convert them into g-code. We're using Printrun, as our host, which sends the data into the printer. And inside of the printer we're using Sprinter as the firmware.
But, in the "not too distant future," Hartkop said his company is going to develop its own host software. While it will have an interface specific to the Mini Metal Maker, even this in-house developed software will be open source at its core.
"We want this to be open enough for people to really experiment with and make their own," Hartkop said.
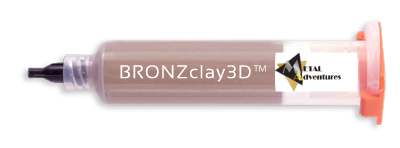
Bronze clay blended specifically for the Mini Metal Maker. Source: David Hartkop.
Mini Metal Maker has worked closely with Metal Adventures, the biggest sellers of bronze and copper metal clays, to produce blends of clay specifically designed to work with Mini Metal Maker. The clay can be preloaded in 50-gram cartridges and be used with different sizes of extruder nozzles.
Time for production
After building the initial prototype for Mini Metal Maker, Hartkop took advantage of the growing interest in crowdfunding and set out to raise $10,000 to fund his efforts to build a production version of the Mini Metal Maker. He more than tripled his goal, raising about $35,000. After a successful campaign, he was able to finish the production version of the Mini Metal Maker.
Now Hartkop is returning to Indiegogo with a bigger vision. In order to "move production out of our basement and onto a factory floor," Hartkop is aiming to raise $150,000. Prizes for contributors range from Mini Metal Maker t-shirts to a complete and assembled production version of the printer.
Funds raised will go toward software development, setting up a professional build space, and factory tooling.
Mini Metal Maker's first production run of 30 units, displayed at Pueblo, CO Rawlings Library. Source: David Hartkop.
Harkop detailed the goals on the Mini Metal Maker Indiegogo campaign home page:
There are several hurdles to overcome before this can happen, including software development, tooling-up, and licensing. It is our goal to create a user friendly host program that will make the user experience as direct and creative as possible. Tooling up for production involves creating shop drawings, jigs, dies and CNC programs with local Colorado manufacturers. Finally, there are several permit and licensing hurdles involved with physical equipment manufacture.
Hartkop wants to bring the Mini Metal Maker to market for a price around $1,500 -- the same amount contributors to the Indiegogo campaign have to donate to receive one as a contributor prize.
How big is the market for Mini Metal Maker?
Does the Mini Metal Maker have the potential to appeal to the same niche of consumers forking out cash for consumer 3D printers like 3D Systems' (DDD 29.54%) Cube or Stratasys' MakerBot? Probably not. But Hartkop does have an ambitious vision of the Mini Metal Maker's addressable market, calling it a $2.2 billion market -- even with the requirement of a kiln.
It's also worth noting that even if the Mini Metal Maker captured a tiny fraction of the same market for MakerBot and Cube printers, it could pay off handsomely for Hartkop. Consider: 3D Systems' revenue in its consumer segment, which includes sales of its Cube series 3D printers and Sense 3D scanners, was $43 million in 2014, up from $35 million in 2013. And Stratasys has sold 80,000 MakerBot units to date.
Hartkop is a testament to the maker culture
The development of the Mini Metal Maker offers a useful look at how 3D printing technology is playing integral roles in helping designers, creatives, and inventors scale their activities.
In the video below, Hartkop looks back at the development of the Mini Metal Maker.
Going forward, Hartkop says it's likely that the MakerBot will be used for production of the Mini Metal Maker itself, explaining that utilizing this new technology is actually more cost effective than traditional injection molding for Mini Metal Maker's scale of production.
It's still not clear whether the Mini Metal Maker will appeal to hobbyists and makers. But whether Hartkop hits his $150,000 target for funding or not, he says Mini Metal Maker will continue toward its goal of bringing the 3D printer to market.
The Mini Metal Maker highlights the intriguing intersection of desktop 3D printers and metal. Is Hartkop's attempt to address this market only the beginning?