Despite the fastest home-price growth in decades, demand for homes hasn't slowed. Homebuilders are amping up to try to meet demand, but supply chain issues and labor shortages are slowing deliveries, leaving home prices to continue running rampant. Supply is the number-one way to curb the shortage and tackle high home prices, but with traditional builders at capacity, some are at a loss for what to do.
Thankfully, there could be a much cheaper and faster solution that could directly address the current housing crisis: 3-D printed homes.
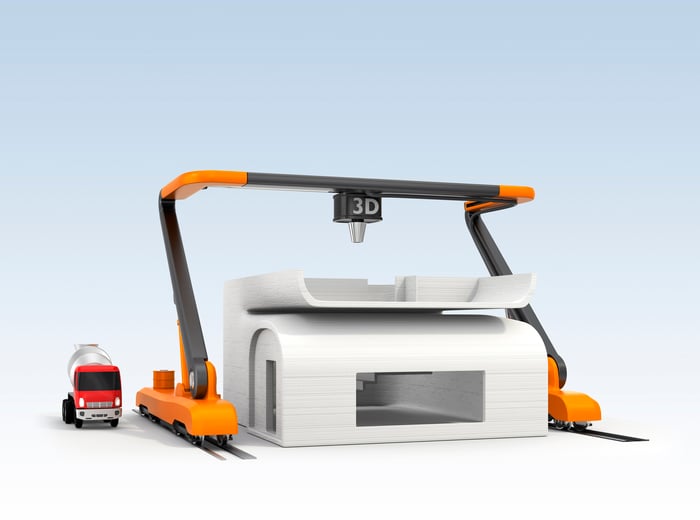
Image source: Getty Images.
What is a 3-D printed house?
A 3-D printed house uses a computer and specialized equipment to "print" a home's frame. Unlike a traditional home that uses wood or blocks to frame a house's walls and create the rooms of a house, a 3-D printer uses concrete in layers to build the floor plan. It functions exactly the same as the wood or block and can be made into almost any layout a designer or buyer wants. The cement can be finished for a traditional look or left exposed for a trendy feel and can vary in size from a tiny house up to a comfortable single-family home.
The technology, which may sound like it's from a futuristic episode of the Jetsons, is actually happening right now in real life. A 3-D printed 1,400- square-foot three-bedroom, two-bath home with a two-and-a-half-car garage recently sold for just under $300,000 in New York. Companies like Icon, Mighty Buildings, and Printed Farms are 3-D printed homebuilders based in the United States and have been building permitted and inhabited homes for several years now, with entire communities now constructed entirely from 3-D technology.
Most of the homes qualify for net-zero designation and are built to last being made of durable materials. And since these 3-D printed homes can be assembled with a crew of just two or three builders, and depending on the size of the home, they can be built in as little as 24 hours up to a few days. This is a viable way for homebuilders and real estate investors to tackle and address the current housing shortage and affordable housing crisis head on.
A solution to the affordable housing crisis
States across the nation are experiencing tough scenarios where low-income households are unable to afford appropriate housing. States like California, Oregon, Nevada, and Florida have less than 30 affordable rentals available for every 100 low-income renters. And even median-income homebuyers are feeling the pressure. The Housing Opportunity Index calculated by the National Association of Home Builders reported that just 57% of new homes built in the second quarter of 2021 were affordable to families earning the median national income; this is the lowest number since 2012.
3-D printing looks like it might be able to meet this need by creating quality homes at a reasonable price to fit most needs. The cost to build an average three-bed, two-bath house is between $250,000 to $320,000. A 3-D printed home costs around 40% less, averaging between $140,000 to $240,000. If a smaller home will work, it could be even less. Icon was able to make 500-square-foot houses for just $5,000 a piece for a project in Peru. Not to mention building a 3-D home requires a fraction of the time it takes for a traditional build, which can range from one to two months or longer.
There are limitations with 3-D building, but the technology is rapidly developing, and it's likely only a matter of time until these hurdles are overcome. Taking into consideration the affordability, the speed at which they can be built, and adaptability from the simplest to the most luxurious of homes, these 3-D printed houses seem like they could be the new era of homebuilding.