Long body repair times are unfortunately all too common for Tesla (TSLA -1.69%) customers. Third-party body shops often attribute delays to waiting on parts from Tesla, while Tesla in some cases says the body shops are responsible for the delays. My own body repair experience was terrible, lasting a couple days shy of eight months, and Tesla's response provided to Electrek mostly attempted to pin blame on the body shop.
Beyond my specific case, the broader issue is that Tesla's support infrastructure for body repairs is strained. But the good news is that Tesla is planning on making some much-needed improvements to how repairs are handled.
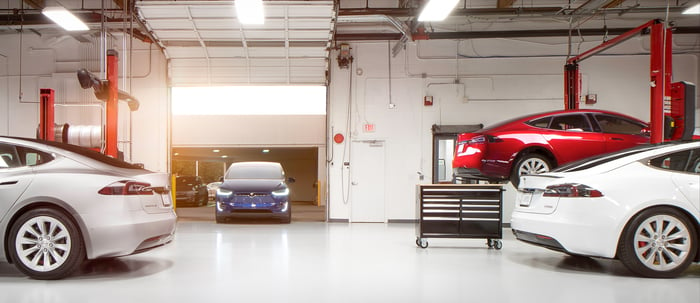
Image source: Tesla.
"applying brute force"
In a thread on Tesla Motors Club regarding my article, Tesla President of Global Sales and Service Jon McNeill posted a response and outlined a "roadmap" for improvement. McNeill noted two important things that Tesla is planning on doing to improve the situation (emphasis added):
We know from complaints that the body shop experience needs to get a lot better -- and fast.
What the service team has done so far is a roadmap of how we're going to fix the autobody experience. Wait times for appointments measured in hours and a handful of days currently. We're providing same-day service from the Bay Area to Oslo and everywhere in between. In fact, almost 20% of jobs in our flagship center in Palo Alto are handled before the customer can finish their cup of coffee (yes, you read that correctly).
Thankfully, only a handful of our owners experience accidents each year. Since customers schedule and interface with the body shops on their own, we're largely blind to the service pace.
Most of the customer complaints about body shops mentioned parts, so we focused on this issue. To date, we've reduced backlog by over 80%.
Even though we reduced part wait times, we continued to dig into the body shop complaints. What we found was astounding -- cars sat at body shops for weeks and sometimes months before the body shops took action and, more often than not, the body shops blaming Tesla for parts delays were the very shops that hadn't even ordered parts or started the repair.
We are applying brute force to this immediately. We will have individuals on our team personally manage each car on behalf of our customers that are in 3rd party body shops.
We're also going to increase our approved shop count by 300 over the next few weeks as well as eliminating poor performing shops.
If you have an issue with a shop, please PM me directly and our team will advocate and manage your repair.
Tesla owners will get the service they expect from us – period.
Thanks to the entire service team for their commitment to setting the highest standard for service in the industry,
Jon
Part of the issue is that since these are third-party body shops, Tesla has less visibility into the repair timelines. In order to mitigate this, Tesla will have employees manage the repair to ensure that everything is proceeding promptly. Having an advocate should relieve customers of having to try to navigate the repair. Perhaps more importantly, Tesla is preparing to add 300 authorized body shops to its network in coming weeks, which should help alleviate backlogs at body shops. It's not clear how many third-party authorized body shops Tesla currently has, but adding more will certainly help.
Strengthening the customer support infrastructure is extremely important ahead of Model 3's launch later this year. Tesla has learned its lessons from making Model S and Model X overly complicated, which is why it is taking a more holistic approach to Model 3 by designing the car from the beginning for both manufacturability and reparability.
Tesla is planning on ordering enough parts from suppliers to start producing 1,000 Model 3 vehicles per week in July, and this will quickly ramp to 2,000 per week in August and 4,000 per week in September. By the end of the year, Tesla hopes to be producing 5,000 per week, which would translate into an annual run rate of over a quarter million vehicles as it enters 2018. In contrast, Tesla produced approximately 84,000 vehicles in 2016. That's a lot more vehicles on the road to support, so getting ahead of service and repair times will be a key factor in whether or not the mainstream model succeeds.