In a previous column, I offered up my thoughts on Apple's (AAPL 0.63%) latest low-cost iPad (marketed simply as iPad). In a nutshell, Apple built a much more cost-effective version of its iPad Air 2 to allow it to attack the $329 price point, while at the same time keeping a reasonable margin structure.
In that article, discussing how Apple managed to cut costs in going from the iPad Air 2 to the new iPad, I made the following claim:
For example, it uses the A9 chip, which is certainly cheaper to produce than the A9X found in the iPad Pro and is almost certainly cheaper to produce than the older A8X found inside of the iPad Air 2.
The former statement (vis-a-vis the A9 and A9X) needs little justification, as the A9X is simply a more complex version of the A9. However, I feel that the comparison of the A9 and A8X cost structures is something that's probably worth justifying, and below, I intend to do just that.
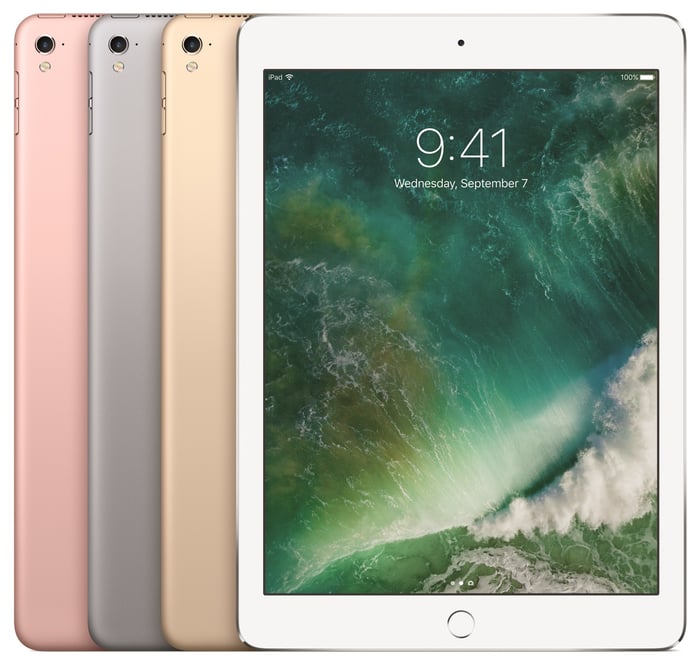
Apple's iPad Pro lineup. Image source: Apple.
Understanding what drives chip costs
In very basic terms, there are a few major factors that drive chip costs. The first is the cost of silicon wafers -- this largely depends on their manufacturing costs, and the profit margin that the contract chipmaker selling the wafers is hoping for. Typically, the more advanced a manufacturing technology, the more expensive the underlying silicon wafers are.
The next is chip size: All other things being equal, a larger chip is more expensive to build than a smaller chip. This is because in such a scenario, silicon-wafer size and cost are fixed, meaning that for a given wafer cost, a chipmaker can produce fewer total chips. Not only that, but yield rates of larger chips -- again, all else being equal -- are lower than yield rates of smaller chips (here's a discussion of the economics of silicon wafers).
Applying this to A8X vs. A9
The Apple A8X is manufactured using Taiwan Semiconductor Manufacturing Company's (TSM 0.24%) 20-nanometer manufacturing technology. The A9 is sourced from both TSMC and Samsung (NASDAQOTH: SSNLF) and is built using their respective 16-nanometer and 14-nanometer technologies.
The A8X chip measures in at 128 square millimeters; the Samsung-built A9 comes in at 96 square millimeters, and the TSMC-built A10 measures 104.5 square millimeters.
The 14/16-nanometer technologies upon which the A9 is built should be a bit more expensive than the one used to build the A8X (the "16-nanometer" technology used here can be thought of as simply a more advanced variant of the 20-nanometer, rather than an all-new technology), but the much larger die size of the A8X, relative to either A9, more than likely offsets the slight extra cost associated with the 14/16-nanometer technologies.
The A9 is cheaper and better
The nice thing about Apple's choice of the A9 for the low-cost iPad is that it's not only probably cheaper to manufacture than the A8X, but it's also a genuinely better processor. The A9 has faster processor cores than the A8X does (though the A9 has two and the A8X has three) and, per the 3DMark Ice Storm graphics performance test, a faster graphics processor than the A8X offers.
I believe that the performance and user experience that the new iPad should deliver with the A9 will be superior to what a hypothetical low-cost iPad with an A8X could have delivered.
Talk about a win-win!